Benefits & drawbacks of bathroom pods for your next multi-family construction project
Bathroom pods are complete, prefabricated bathrooms that can be added into multi-family apartment building projects during construction. In the factory, the pods are fully fitted with bathroom fixtures and MEP, and shipped to the jobsite for installation. They can be custom-designed so they fit perfectly into your project, both in terms of physical design and budget.
Christine O’Callaghan is an Off-Site and Prefabrication Consultant at Off-Site Engineering Solutions FZE. She shared some information about using bathroom pods, which may be helpful if you’re thinking of using them on your next multi-family project.
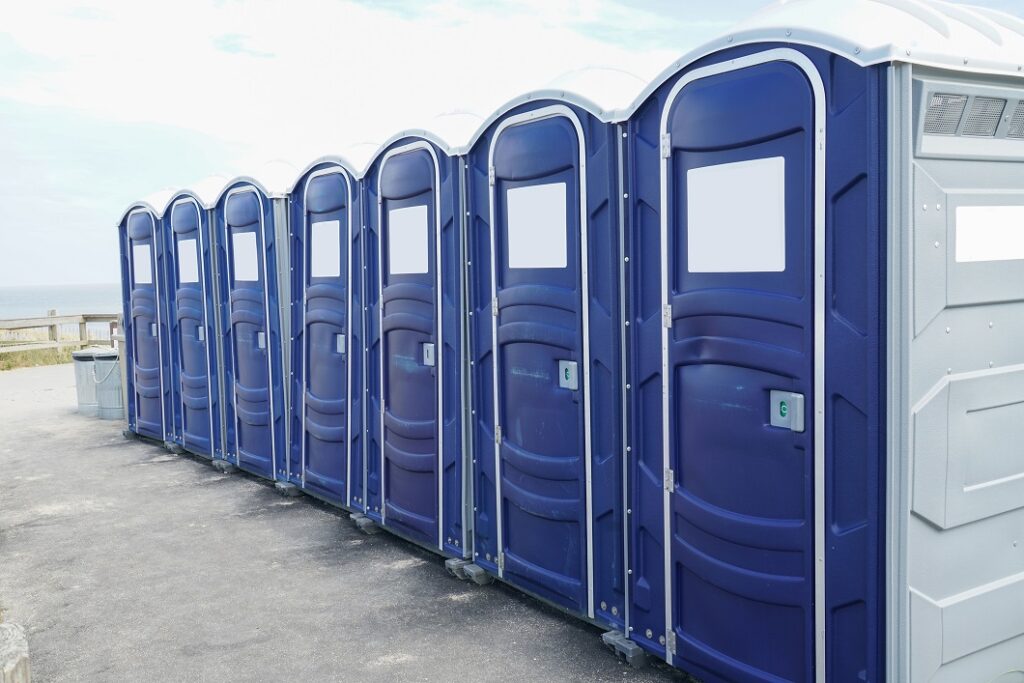
Benefits of using bathroom pods
Speed — Pods are built offsite while the jobsite is being prepared, the foundation poured and cured, and the framing of the building goes up. “Bathrooms are completed before the enabling work on site,” O’Callaghan explains. “This means the complete bathroom can be installed as soon as possible with no knock-on delays.” There’s no need to wait for the trades to finish the bathrooms on the first floor before moving on to the bathrooms on the second floor. The bathrooms are ready when you’re ready to install them. A shorter construction period means earlier occupancy, quicker to revenue, and less interest on construction loans.
Less risk — There’s no need to stockpile bathroom components on site and distribute them up to multiple floors. Because bathroom components don’t have to be stored on site and schlepped up to each floor to be installed, there’s less risk of damage to the bathtubs, mirrors, cabinets, and so on. (A shorter punchlist is always welcome, right?) All the components are stored indoors at the offsite manufacturing plant until they’re ready to be installed inside the pods. They stay safely inside when the pods are transported and installed into your apartment building on site.
Quality — “Bathroom pods are produced in factory-controlled conditions, so they’re completely unaffected by the weather,” O’Callaghan says. She adds that “the standardized conditions promote more precise planning and scheduling, resulting in pods that are on time, fully finished, and quality assured.” Pods are wrapped in heavy-duty shrink-wrap for transportation. From a reliable pod manufacturer, every bathroom should be high quality, reducing the likelihood of rework. As with any other major supplier, it’s a good idea to ask past customers about their experiences with the pod manufacturer.
Simpler — No need to coordinate all the products that need to be installed and all the tradespeople needed to install them. Since all the plumbing and electrical work, and the installation of the fixtures happens offsite, this reduces your headaches. You deal with just one supplier — the offsite pod manufacturer — simplifying procurement and lowering the risk of delays. “Bathroom pods essentially deliver all the potentially high-value contents of numerous boxes, crates, bags, and packages to the site in a single ‘quality assured’ box,” O’Callaghan says.
Less concrete — O’Callaghan says that an often overlooked advantage of using bathroom pods is “the reduction in slab and screed materials in the areas where the pod will ultimately sit. A typical pod floor will replace between one and two cubic meters of structural reinforced concrete.”
Drawbacks of using bathroom pods
Planning — Traditionally, bathrooms can be finalized fairly late in the construction process. But using bathroom pods requires upfront planning. “Early design freeze is critical to the successful integration of bathroom pods,” O’Callaghan says. They need to be carefully designed so they’ll fit seamlessly into your building. The manufacturer will need the designs early in the process so they can order components and start manufacturing.
Cash flow — “There will also be a significant commercial impact on the project cash-flow due to the necessary early procurement of typically high cost fitting-out materials,” O’Callaghan says. Of course, the more high-end the finishes are, the greater this impact will be.
Standardization — To reap efficiencies, it’s best for the bathrooms in your apartment building to be as similar as possible — either exactly the same, or perhaps mirrored. If you’re planning a number of different bathroom designs, a pod approach makes less sense. “The repetitive nature of the design is key to the overall efficiency. The positive impact of using bathroom pods rises as the number of design variations is reduced,” O’Callaghan explains.
Design changes — During traditional construction, bathroom design details might not be finalized until quite late in the construction process, and changes can be made to the bathroom design during construction. Nevertheless, such changes “inevitably incur additional costs, time delays, waste, or general inefficiencies,” O’Callaghan points out. “For exactly the same reasons, pod interior designs can ultimately be changed after work has begun — but again this will result in inefficiencies or compromised quality of finish,” O’Callaghan says. When using bathroom pods, one thing is set in stone, though: “Their footprints cannot be changed. The basic structural parameters of the pod will be the first design feature that is locked in,” she says.
How many builders are using bathroom pods on their projects?
In their publication, Prefabrication and Modular Construction 2020, Dodge Data & Analytics reported that 72% of surveyed GCs and construction managers made “some use of factory-made turnkey building units (e.g., bathroom pods, utility rooms, exam rooms, etc.) over the past three years, although most say that has taken place on less than 25% of their projects.”[1] Unfortunately, I couldn’t find statistics that related specifically to builders’ use of bathroom pods (as distinct from other kinds of prefabricated pods).
Have you used prefabricated bathroom pods in your multi-family apartment projects? Do you think the advantages outweigh the drawbacks?
Learn more about using bathroom pods in your projects:
Tips for designing and building with bathroom pods
15 tips for specifying bathroom pods
Insights into the increasing demand for bathroom pods
Consigli Construction Making the Most of Modular (case study)
[1] Dodge Data & Analytics: Prefabrication and Modular Construction 2020, p.34
Leave a comment