The world needs greener concrete. Why? And How?
Concrete has long proven its usefulness as a building material. It’s the most commonly used human-made substance on the planet and twice as much concrete is used in construction as all other building materials combined. And we’re producing more and more of it all the time.
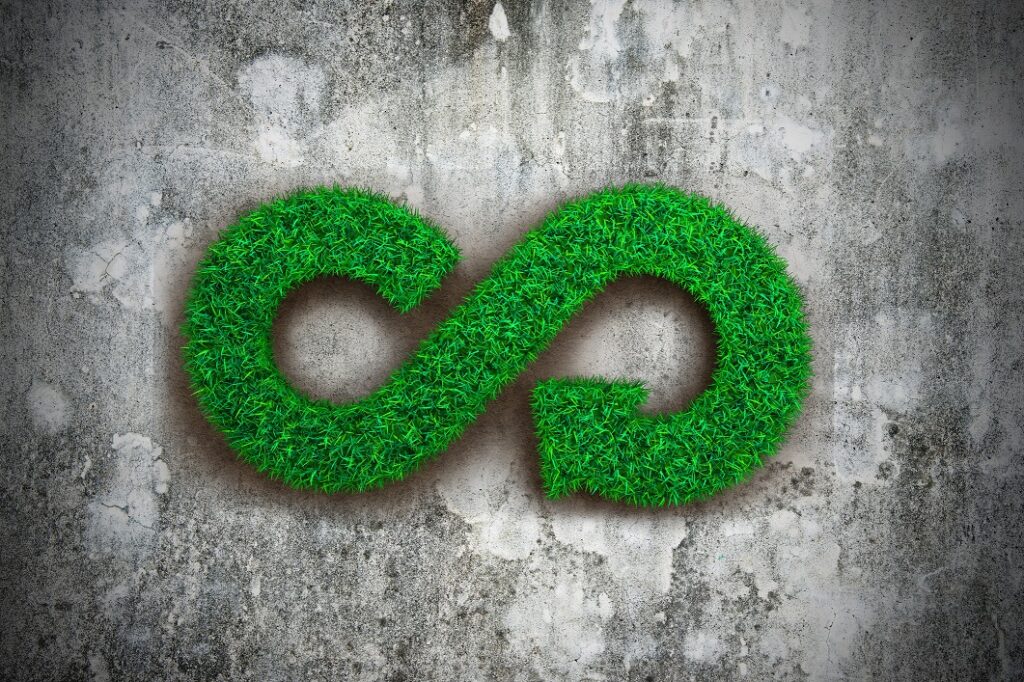
Why is concrete bad for the environment?
The problem is that making cement — an essential ingredient of concrete — is incredibly harmful to the planet. Cement production accounts for about 8% of global carbon dioxide emissions. It’s the largest single industrial CO2 emitter.[1] The CO2 emissions come from both combustion of fuels to power cement kilns and also from the release of the stored carbon from the limestone that’s used:
“Making the cement is the most carbon-intensive part: it involves using fossil fuels to heat a mixture of limestone and clay to more than 1,400 °C in a kiln. Also, when limestone (calcium carbonate) is heated with clays, roughly 600 kilograms of carbon dioxide is released for every tonne of cement produced.”[2]
According to the Global Cement and Concrete Association, heated limestone is responsible for about 60% of the emissions, and 40% is due to burning the fossil fuels to heat the kilns (and for other plant processes).[3]
Taking action
The cement and concrete industry has recognized that something needs to be done, and claims to have reduced the ‘carbon intensity’ of cement by 20% since 1990.[4] (This means the production of one tonne of cement results in lower CO2 emissions than producing one tonne of cement did in 1990. But since we’re producing so much more of the substance, overall emissions from the production of cement have not declined.) In 2017, researchers reported that manufacturing 1 tonne of cement released approximately 1 tonne of CO2.[5]
The Global Cement and Concrete Association has committed to delivering carbon-neutral concrete by 2050. Their goals have been third-party verified by the organization, Science-Based Targets — a partnership between the Carbon Disclosure Project, the United Nations Global Compact, the World Resources Institute, and the World Wide Fund for Nature.
Here’s where the association lays out its plans to deliver carbon-neutral concrete: Getting to Net-Zero.
In addition to industry-led action, some jurisdictions are implementing low-carbon concrete policies, to have an impact sooner rather than later:
“As the public sector procures 39% of all concrete used, procurement that prioritizes lower-carbon products will create demand that accelerates the transition to net zero or even net negative concrete. Without this economic impetus, these technology solutions may emerge too slowly to meaningfully contribute to the carbon removal target.”[6]
In North America alone, CarbonCure’s Senior Director of Government Affairs, Eric Dunford, told me by email that at least the following states and cities are taking action:
Enacted:
- New York State
- Colorado
- California (cement requirements)
- Portland, Oregon
- Langford, British Columbia
- Honolulu, Hawaii
Proposed:
- New Jersey
- Virginia
- Oregon
- Washington
For more information on some of the above policy actions, see The Time for Policy Action is Now. Dunford, says:
“From California and Hawaii to New Jersey and New York, it’s exciting to see policymakers from coast to coast recognizing the opportunity to advance the production and procurement of low-carbon concrete with smart policies. These are business-friendly, common sense solutions attracting bipartisan support, developed in collaboration with industry, that will catalyze the transition to a low-carbon economy and ensure a more sustainable future.”
How can the carbon footprint of concrete be reduced?
Various ways have been proposed to reduce the carbon footprint of concrete — and some are actually being implemented in the real world. Below is just a handful of the possibilities. (Companies mentioned are examples to illustrate the various possibilities; this shouldn’t be taken to be an endorsement. I don’t have expertise in climate science, chemical engineering, or any other relevant discipline — and so I’m not in a position to make any recommendations!)
Building design
This idea is a very simple one: Design buildings so they use less concrete. This might mean making buildings smaller, or using the same space more efficiently. An example might be building a fourplex instead of four single-family homes.
It could mean using alternative materials, whenever possible. Of course, for this to have a beneficial impact, the materials would have to perform as well as concrete and have a lower carbon footprint.
It could mean designing buildings so they use less concrete per square foot (which may require stronger concrete).
Read more:
Seven Ways to Use Less Concrete and Save Money on your Projects
These ingenious floors use 70% less concrete and 90% less steel
Alternative fuels
Not using fossil fuels to heat the kilns and switching to lower-carbon (e.g. biomass) or carbon-neutral (e.g. solar or wind generated electricity) alternatives may reduce the carbon footprint of concrete.
Heliogen is a company that’s working on using solar heat to achieve the temperatures of over 1000°C that are required to make cement. Their process has been described as follows: “Sunlight is captured and focused into either a long, pipe-like tube or a tower-mounted receiver to generate heat, like the supersized version of a kid frying a bug under a magnifying glass.”[7]
Carbonation
What if waste carbon dioxide produced during industrial processes was captured instead of being released into the atmosphere? What if it was then permanently sequestered in concrete, never to be released, even after demolition? What if being injected with CO2 actually made concrete stronger?
“Another possibility is to pump the captured CO2 into concrete itself, locking it up forever — which might also improve the properties of the resulting material. The injected CO2 reacts with calcium ions in the cement, producing more calcium carbonate, and potentially making the concrete able to withstand larger loads.”[8]
CarbonCure is an example of a company taking this route. Their technology injects captured waste CO2 into fresh concrete. The CO2 undergoes a chemical process inside the concrete to form a calcium carbonate mineral. This is a permanent chemical change and even when the concrete is demolished, there is no way for CO2 to escape into the atmosphere. The resulting concrete is stronger than ordinary concrete.
“The compressive strength of carbonation-cured concrete was more than 10% higher than that of moisture-cured concrete at the same age.”[9]
Because of this increased strength, the concrete needs a lower percentage of cement, further reducing its environmental impact.
Different ingredients
CarbiCrete has developed technology to create concrete without using cement. Instead of cement, steel slag (a by-product of steel manufacturing) is used as a binder. The mixture of aggregate, water, and slag is poured into concrete masonry units [CMU] molds as usual. Captured CO2 is used to cure the concrete.
A 2016 study showed that this process for CMUs:
“consumes no natural resources, produces no wastes, is capable for carbon sequestration and is a clean production. The slag-bond concrete block is a carbon-negative product. In addition, slag-bond concrete block exhibited better mechanical and durability properties compared to the commercial cement block. The cost analysis suggests that slag-bond concrete blocks can be made at a lower cost compared to the commercial cement block if they are mass produced.”[10]
Conclusion
The science behind improving the carbon footprint of concrete is complex, and I don’t pretend to be an expert. However, it’s reassuring to see progress is being made — even though we can all agree that it needs to be faster. Everyone with influence in the construction industry can and should help us leave a healthier planet for future generations.
CarbonCure’s Senior Director of Government Affairs, Eric Dunford, says,
“The embodied carbon challenge is immense. We need both the public and private sectors pulling together. Architects, engineers, and contractors can be part of this solution by adopting performance-based specifications that prioritize low-carbon concrete. This will send powerful market signals, accelerating innovation and sustainability across the concrete industry.”
Further reading:
Concrete: the most destructive material on Earth, The Guardian, 2019
Concrete needs to lose its colossal carbon footprint, Nature, September 2021
A net-zero world needs zero-carbon concrete. Here’s how to do it, World Economic Forum, July 2021
How do you make concrete more environmentally friendly?, CBC, June 2021
Cut Carbon and Toxic Pollution, Make Cement Clean and Green, Natural Resources Defense Council, January 2022
Climate change: The massive CO2 emitter you may not know about, BBC, December 2018
Green growth avenues in the cement ecosystem, McKinsey, December 2021
[1] Toward electrochemical synthesis of cement—An electrolyzer-based process for decarbonating CaCO3 while producing useful gas streams, PNAS, Leah D. Ellis et. al., September 2019
[2] Concrete needs to lose its colossal carbon footprint, Nature, September 2021
[3] https://gccassociation.org/concretefuture/our-path-to-net-zero/
[4] A net-zero world needs zero-carbon concrete. Here’s how to do it, World Economic Forum, July 2021
[5] Towards sustainable concrete, Paulo J. M. Monteiro et. al., Nature Materials, June 2017
[6] Deploying Low Carbon Public Procurement to Accelerate Carbon Removal, Eric Dunford et. al., Frontiers in Climate, September 2021
[7] This company wants to make steel and cement with solar power. Here’s how, Grist, November 2019
[8] Concrete needs to lose its colossal carbon footprint, Nature, September 2021
[9] The Performance of Carbonation-Cured Concrete, Materials, Zhen Li et. al., November 2019
[10] Production of cement-free construction blocks from industry wastes, Mehrdad Mahoutian et. al., Journal of Cleaner Production, November 2016